Allowable Pipe Stress Based on ASME B31.3
The study of stresses in a piping system is referred to as pipe stress analysis. It includes calculations that take into account static and dynamic loads such as deadweight (the pipe's weight, including fluid, fittings, and other components), internal and external pressure, thermal loads (due to temperature changes), seismic loads, wind loads, vibration, water hammer, steam hammer, slug force, PSV reaction force, and so on. Not all loads are appropriate in every system; for example, thermal loads are not applicable if the system temperature is assumed to remain constant. The design foundation determines the applicable loads.
For conducting the stress analysis of a piping system, the allowable stress of the material is an important parameter. According to code and standards, working stress in the pipe system should not exceed the material's permitted stress. It is the stress ratio commonly employed in the piping system. The stress ratio compares the actual operating pressure in the piping system to the maximum stress allowed by code and standard.
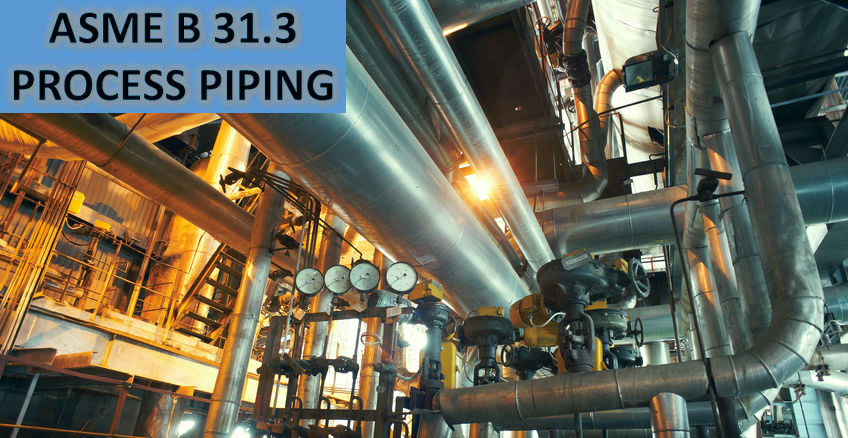
Each code has a different value for allowable stress. Through this article, I’ll discuss the acceptable pipe stress following ASME B31.3 and the various criteria for allowable stress and allowable stress for various materials following ASME B31.3 used by piping stress analysis services consultants.
ASME B31.3 Allowable Stress for Piping Materials
Because they are documented in codes like ASME 31.1, 31.3, sec III, the fundamentally allowed stresses are often known as code stresses. These are the basic permissible pressures for the basic sustained loads as design stresses. The design stresses are changed from these fundamentally allowed pressures for additional loadings using factors and/or combinations.
For materials other than bolting materials, cast iron, and malleable iron, the fundamental allowed stress levels at a given temperature are the lowest of the following:
- One-third of ultimate strength at room temperature or one-third of ultimate strength at temperature, whichever is lower. Instead of 1/3, a 1/3.5 factor is used in B31.1 and Class 2 nuclear pipes.
- Except for austenitic stainless steel and nickel alloys with similar stress-strain characteristics, the lower of 2/3 yield strength at room temperature and 2/3 yield strength at temperature is taken.
- A creep rate of 0.01 percent every 1000 hours is 100 percent of the average stress.
- After 100,000 hours, 67 percent (2/3) of the average stress for rupture.
- After 100,000 hours, the stress must be at least 80 percent of the minimum stress for rupture.
- The lower of 2/3 of S and 90 percent yield strength is taken at temperature for austenitic stainless steels and nickel alloys with identical stress-strain characteristics.
The pipe material can be expressed in a safe condition per ASME 31.3 if the stresses it is subjected to match the following criteria:
- Sustained Load: The consequence of longitudinal stress (SL) in each component of a piping system due to a sustained load, such as internal load or pipe load weight, shall not exceed the value of the multiplication between Sh and W. Sh is the maximum stress that a pipe material can withstand at its working temperature. In the pipe manufacturing process used by piping stress analysis services consultants, W is the reduction factor of the welding connection. If the longitudinal connection type is utilized in the pipe manufacturing process, W equals 1.0. In a piping system used by piping stress analysis services consultants, the displacement stress range (SE) should not exceed the permissible displacement stress range (SA), which can be calculated as follows:
SA = f(1.25 Sc + 0.25 Sh)
Where f is the stress range factor, Sc denotes the pipe's maximum allowed stress at its lowest working temperature, and Sh is the maximum stress that a pipe can withstand at its highest working temperature.
- Occasional Load: When the longitudinal stress resulting from continuous load and all loads produced by occasional loads, such as wind load and seismic load, is multiplied by the allowed stress of pipe at maximum working temperature, the resultant should not exceed the value of 1.33. (Sh). The Sh value must be multiplied by factor quality casting for casting material (Ec). Wind and seismic loading do not usually occur simultaneously; hence, only one of those loads is calculated based on the environmental conditions in the pipe stress analysis.
- Thermal Expansion Load: The tension caused by thermal expansion ranges from bending stress and torsional stress caused by thermal expansion. According to the following equation, range expansion stress should not exceed allowed stress SA:
SE = √(Sb2 + St2) ≤ f(1.25 Sc + 0.25Sh)
Bending stress and torsional stress are represented by Sb and St, respectively.
Allowable Stresses for Pipes of Different Materials
This article uses a few examples to demonstrate the following requirements.
- Carbon Steel Pipe: Let's look at ASTM A106 GrB seamless pipe as an example. The provided minimum tensile strength is S = 60ksi, and the specified minimum yield strength is S = 35ksi.
Using the preceding rules,
The lower of (1/3) of S = (1/3)*60ksi = 20ksi and (2/3) of S = (2/3)*35ksi = 23.3ksi equals 20ksi.
20ksi is the lesser of the two values. As a result, from the lowest temperature to 400°F, the maximum allowed stress is 20ksi. This translates to a safety factor of 3 for ASTM A106 GrB pipe in terms of the mandated minimum tensile strength S.
- Stainless Steel Pipe: Let's look at the ASTM A312 TP316 pipe as an example. The specified minimum tensile strength is S = 75ksi, and the specified minimum yield strength is S = 30ks.
The lower of (2/3) of S = (2/3)*30ksi = 20ksi and
(90 percent) of S = (0.9)*30ksi = 27ksi.
20ksi is the lesser of the two values. As a result, the maximum permissible stress is 20ksi from 0 to 300°F. For ASTM A312TP316 pipe, this translates to a safety factor of 1.5 in the prescribed minimum yield strength S.
- Nickel Alloy Pipe: Finally, use the ASTM B444 UNS N06625 pipe as an example. The specified minimum tensile strength is S = 120ksi, and the specified minimum yield strength is S = 60ksi.
The lower of (90 percent) of S = (0.9)*60ksi = 54ksi and
(2/3) of S = (2/3)*60ksi = 40ksi equals 40ksi.
40ksi is the lesser of the two values. As a result, from the lowest temperature to 300°F, the maximum allowed stress is 40ksi. This translates to a safety factor of 1.5 for ASTM B444UNS N06625 pipe in terms of the prescribed minimum yield strength S.
Allowable Stress VS Temperature in Different Materials
- Carbon Steel Pipe: As mentioned earlier, the allowed stress for ASTM A106 GrB pipe is (1/3) of tensile strength up to 400 °F. The allowed stress will be lower of (2/3) of yield strength and (1/3) of tensile strength at the appropriate temperature as the temperature rises above 400 °F and up to 700 °F. Allowable stress is controlled by (2/3) of yield strength rather than tensile strength at temperatures over 400 °F. The slope of permitted stress versus temperature increases steeper at temperatures beyond 700 °F, implying a greater drop in allowable stress with temperature. The allowed stress at temperatures exceeding 700°F is determined by the creep parameters of ASTM A106 GrB pipe material.
- Austenitic Stainless-Steel Pipe: As mentioned earlier, the allowed stress for austenitic stainless steel pipe ASTM A312 TP316 pipe is (1/3) of tensile strength up to 300°F, as mentioned in the previous section. The allowed stress will be lower (2/3) of yield strength at room temperature, and 90 percent of yield strength at the applicable temperature as the temperature rises above 300°F and up to 1050°F. The allowed stress at temperatures between 300°F and 1050°F is determined by a percentage of yield strength rather than tensile strength. The slope of permitted stress vs. temperature increases steeper at temperatures above 1000°F for ASTM A312 TP304 and 1050°F for ASTM A312 TP316, implying a quicker drop in allowable stress with rising temperature. The allowable stress is based on the creep qualities of stainless-steel material at temperatures above the elastic limits.
- UNS N06625 Nickel Alloy Pipe: As mentioned in the previous section, the allowed stress for nickel alloy ASTM B444 UNS N06625 pipe is (1/3) of tensile strength up to 200°F, as mentioned in the previous section. The allowed stress will be lower than (2/3) of yield strength at room temperature, and 90 percent at the applicable temperature as the temperature rises above 200°F and up to 950°F. Allowable stress will be determined by a percentage of yield strength rather than tensile strength at temperatures over 200°F. The allowable stress versus temperature slope grows steeper at temperatures beyond 950°F, implying a greater drop in allowable stress with rising temperature. The allowable stress is based on creep parameters of ASTM B444 UNS N06625 pipe material at temperatures over 950°F.
Conclusion
ASME B31.1 establishes minimum requirements for piping systems in electric power plants, industrial and institutional buildings, geothermal heating systems, and central and district heating and cooling systems.