How to Design Control Panels for Hazardous Industrial Settings
Certain industrial settings are classified as hazardous due to the sensitivity of the materials being handled such as fibers, flammable gases, dust, or vapors. This blog classifies hazardous locations, talks about the appropriate placement of control panels, and explains how to design industrial panels for such locations so they don’t pose any risk.
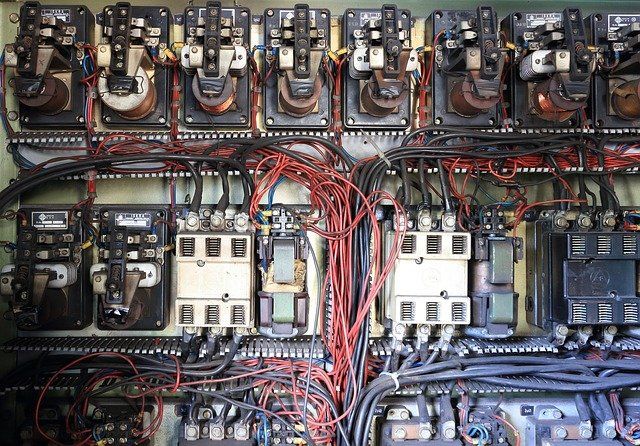
Designing Control Panels for Hazardous Locations
Employees working in hazardous environments rely on the control systems for safe and efficient operations and optimal functioning of equipment. Therefore, control panel design is extremely important for such settings. It calls for careful planning, meticulous designing, and engineering as compared to normal working conditions.
Hazardous Environments
Hazardous environments are defined as areas containing a high concentration of combustible matter that risks ignition, explosion, or electrocution. Such environments are broadly classified into different zones, classes, and divisions as described below:
- Divisions – used to describe the potential of hazardous materials in an area. There are two divisions.
- Division I represents a high concentration of hazardous materials and therefore, a high possibility of explosion.
- Division II indicates a low possibility owing to a relatively low concentration of flammable materials.
- Classes – used to describe the general nature of hazardous materials in a certain area. There are three different classes.
- Class I is defined as an environment where combustible vapors or gases are potentially in a concentration that’s enough to ignite an explosion.
- Class II is defined as an area where the presence of explosive specks of dust or airborne particles is potentially high and there is a considerable risk of potential ignition or explosion.
- Class III is defined as a location with flammable fibers that can potentially result in an explosion, ignition, or both.
- Groups – used to define the specific type of hazardous materials that are typically listed from A through G.
- A is defined as the environment containing acetylene
- B stands for a location containing flammable liquid vapor that may explode when mixed with air such as acrolein, ethylene oxide, butadiene, or propylene oxide
- C represents a setting containing flammable gases, liquids, or vapor such as morpholine, carbon monoxide, cyclopropane, acetaldehyde, or hydrogen sulfide
- D means an environment containing combustible gas, liquid, or vapor that may explode when mixed with air such as gasoline, butane, hexane, natural gas, propane, ethanol, or methanol
- E describes an atmosphere containing explosive metal dust such as magnesium, titanium, aluminum, bronze, zinc, or chromium along with their alloys or other abrasive dust particles that pose a hazard in connection with electrical equipment
- F stands for a location with a high concentration of carbonaceous dust including coal, coke, charcoal, or carbon black with entrapped volatiles that heightens the risk of an explosion.
- G defines an environment containing combustible materials such as chemicals, plastics, flour, grain, wood, starch, or sugar.
Knowing these classifications is crucial for designing industrial control panels to be placed in hazardous locations. Your knowledge and experience have a direct impact on the materials, components, and enclosures used in the designing and engineering of the control panels.
How to Design Control Panels for Hazardous Industrial Settings
Let’s delve deeper into the specifics of how industrial panels are to be designed for ensuring safety:
- Purge Systems: Pressurized systems work by purging the enclosure at the point where the hazardous material resides. It does this by using protective gases that help maintain non-hazardous air around the panel. There are 3 subcategories (type X, Y & Z) of purge systems based on the location of placement. When the air containing hazardous materials is purged, the panel runs safely without any threat of ignition or explosion.
- Explosion-proof Enclosures: Control panel enclosures can be designed in a way that ensures safety from explosions. The design aims to protect the panel from any explosion that occurs because of interaction with any combustible materials present in the environment that could spark a fire.
The enclosure is safely designed to maintain a certain temperature around the panel and its enclosures to avoid any temperature-induced explosion. Most of these enclosures are flame resistant and find application in the oil and gas industry and manufacturing units with a large volume of combustible materials or chemicals.
- Corrosive Environment: NEMA 4X panels can be installed in locations that contain caustic or corrosive materials. These control panels are made up of sturdy materials like polycarbonate, stainless steel, fiberglass, or aluminum for robust protection against extreme temperatures and weather conditions.
Common industries that use these control panels include petroleum, food processing facilities, and clothing industries that deal with strong cleaning chemicals, caustic dyes, or strong disinfectants in their processes.
For industrial environments where the panel may be exposed to liquids or remain submerged, NEMA 6P panels can be installed. They are also used in areas where corrosive dust, dirt, or materials are present.
How an Electrical Engineering Services Company Can Help Ensure Total Safety
An experienced industrial electrical engineering services company has all the knowledge and resources for designing control panels and enclosures for various hazardous environments across a wide range of industries. Working with a team that is well-versed with all the relevant hazardous locations, industry codes & standards and meets all your project's compliance requirements will also save you from the unnecessary costs and complications of rework. Additionally, you get the benefits of error-free designs, optimized estimations, and round-the-clock support for any type of electrical resource requirements.