Key Considerations for Designing Equipment & Piping Layout of Pumps and Vessels
When optimizing the plant layout of any project, it is crucial to ensure that the available space is used to achieve better operability and maintainability. The placement of every component of the process and industrial equipment is important from the standpoint of safety, compliance guidelines, efficiency, and ease of use. This article elaborates on vital design considerations of various equipment and piping layout for pumps and vessels during modularization.
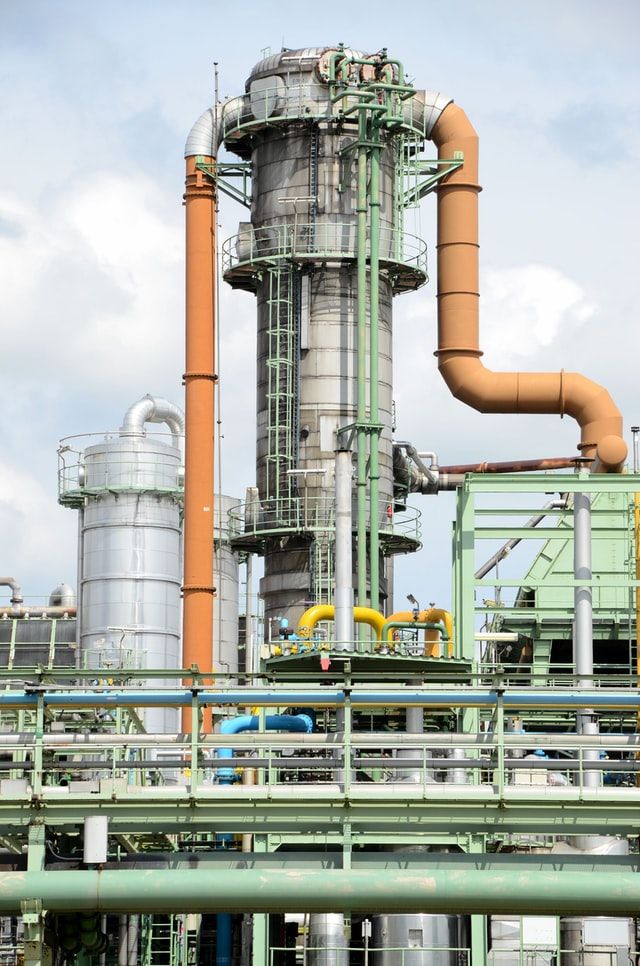
Here are a few standard guidelines to keep in mind:
- Consider aligning the piping and equipment symmetrically to ensure an organized arrangement. For instance, tanks and vessels can be placed in rows to accommodate pipe racks in between.
- Arrange equipment in alignment with the process flow. Doing this will optimize piping runs due to gravitational force.
- For vessels containing hot materials, make sure they have room to expand. Take thermal expansion into consideration.
- Leave adequate space between each component to facilitate safe and easy operations and maintenance. Ideally, a clearance of 3 feet is recommended.
- Ensure that access is available for firefighting and tackling emergencies.
- Fired equipment must also have clear access to facilitate the removal of burners, tubes, fans, and other components.
- All furnaces should be placed upwind and at a safe distance from the processing equipment. To minimize the length of alloy piping, place the tower close to the furnace.
- Vessels can have elevation requirements to boost pump performance.
Different Vessels and Their Unique Needs
Vessels are the key components of chemical processing facilities and refineries. These reactors are subject to constant chemical changes. Separation takes place in accumulators & fractionators. This is why piping engineers need to collaborate with process engineers to make sure everything fits together and functions at peak efficiency.
Horizontal Vessels
Accumulators, drums & receivers are horizontal vessels and so, their design considerations vary drastically in comparison to vertical vessels.
- If the vessel elevation is not having any pump performance issues, then the elevation can be defined by piping layout or process requirements.
- Flare knockout drums and blowdown should be placed in an isolated area of the unit. Ideally, they are to be located at least 25 feet away from process equipment and 50 feet away from heaters to ensure fire safety.
- One end of the vessel can remain fixed, and the other end can be kept sliding. This will ensure proper designing of the foundations and piping saddles.
- Inlet & outlet nozzles can be located at two opposite ends.
Vertical Vessels
Columns, towers & fractionators have common design needs and so, you can:
- Coordinate the ladder and platform locations with the clear drop and piping area.
- The first ladder from the grade can be placed on the side of the pipe rack for easy access by the operator.
- Create easy access to davits & cranes for towers that stand taller than 50 feet.
Pumps and Their Needs to Keep in Mind
Pumps are designed to transport slurries and liquids from one location or component of any equipment to another, using pressure. The material that is being carried can be hot, cold or it can have an ambient temperature. The discharge and suction lines are usually placed at the top or on the side of the pump.
Centrifugal pumps are commonly used in industries. Rotary, diaphragm & reciprocating pumps are also used in commercial settings for particular situations. While most pumps run on electric motors, some are driven by steam turbines for power backup. Diaphragm pumps use compressed air to function.
The main consideration in the pump layout is its placement. Every pump should be placed near the equipment that delivers material to the suction inlet. To minimize friction losses, the suction piping is to be kept straight and short.
Another crucial consideration is the consistency of pump location with the specifications provided by the OEM. These specifications ensure appropriate suction & discharge pressure.
It is recommended to move pumps carrying flammable materials away from pipe racks to limit the possibility of damage in case of fire.
Mechanical engineers must make sure that the location of the pump will:
- Ensure easy access to the pump and motor for repairs, replacements, and periodic maintenance. This facilitates the servicing of cooling systems and pump lubrication along with the areas surrounding bearings and pump seals.
- Prevent potential obstacles in every direction. When everything is installed, none of the components, pipes, or valves should come in the way. Also, make sure that the pump can be removed without having to remove any of the isolation valves.
- Ensure compliance with OEM’s specifications for piping, especially for the straight run suction line. And if the pump is installed in a fire water facility, other codes may be applicable.
Piping engineers must take numerous factors into account when designing the pump’s suction and discharge layout. The following specifications are a sample of industry standards and best piping layout practices.
Pump Suction Piping
Suction piping is typical, one to two-line sizes bigger as compared to the pump nozzle. If the suction line is two sizes larger, it is best to use a block valve that’s one size bigger than the nozzle. Place a drain between the nozzle and the block valve.
The suction piping should be as short as possible to minimize losses due to flow turbulence and friction at the pump. Following API guidelines to ensure a straight run based on nozzle size ensures uniform flow between the flange and the first valve, cross, tee, or strainer. It also reduces the possibility of cavitation.
The forces exerted on the pump nozzles by the suction should also be kept below the OEM’s permissible limits. Some other vital factors include:
- Use long radius elbows to minimize their number
- Install temporary strainers
- Place reducers close to the pump and use eccentric reducers on suction lines
- Avoid high points in suction piping to prevent vapor collection
- Don’t mount any valves on flanges to ensure smooth flow
Pump Discharge Piping
Discharge piping is typically one to two-line sizes larger than the nozzle. A block valve and check valve are placed near the discharge outlet. If the discharge line is two sizes bigger than the nozzle, both the block and check valves should be a size bigger than the nozzle. Again, be sure to stick to the OEM’s specifications and keep the layout well within the allowed limits. Other guidelines include:
- Install the control valve on the discharge side to control flow.
- Place a drain between the block valve and check valve.
- Avoid pockets in places where vapors can accumulate.
- Don’t mount valves on the flanges.
- Provide a bleed in the pressure gauge pipe between the nozzle and valve.
Pumps keep every component of a plant up and running optimally. Teaming up with a leading provider of piping stress analysis services when designing equipment and piping layout for vessels and pumps will offer you many advantages such as:
- Ensuring safety and compliance
- Minimizing the number of pipe layouts
- Enhancing equipment longevity
- Lowering maintenance costs
- Striking a balance between dynamic and thermal support
With vast experience in executing a full spectrum of piping stress analysis services, they offer practical solutions for a wide range of projects, enabling you to define and assess system models quickly and accurately.