Piping material considerations for sour service environment
Sour service is one of the most difficult difficulties in hydrocarbon production, as identified by companies from the oil and gas sector. H2S cracking jeopardizes the integrity of assets and operations.
So, to examine all these vital points, I will discuss the sour service environment, NACE MR O175/ISO 15156 standard, piping material selection variables, H2S cracking mechanisms, and material considerations.
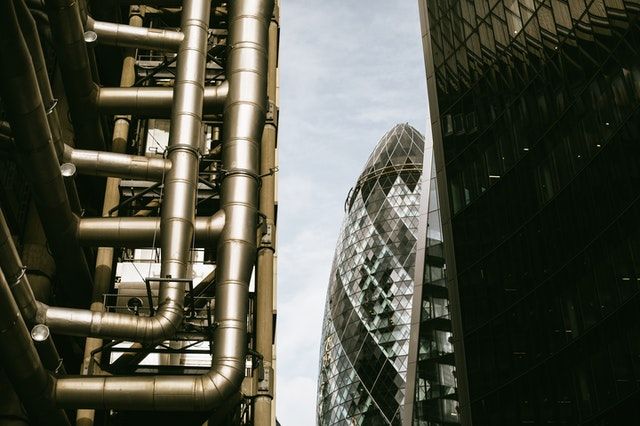
What is Sour Service Environment?
Sour service refers to oil and gas exploration and production conditions with high levels of H2S (hydrogen sulfide), which can cause metallic components to crack. The environment in which it is generated is referred to as the sour service environment. H2S is a highly flammable, explosive gas that, if not handled appropriately, can result in life-threatening scenarios. Even in very low quantities, H2S is lethal. Short-term exposure to H2S concentrations as low as 100ppm (parts per million) can be fatal. This was emphasized by government regulators, health and safety organizations, and industry associations worldwide.
What is NACE MR O175/ ISO 15156 standard?
On the other hand, Petroleum and Natural Gas Industries — Materials for use in H2S-containing environments in oil and gas production is the title of NACE MR0175. It was produced as a guideline of H2S threshold levels over which environmental cracking precautions are considered necessary.
NACE MR0175 is recognized as a standard for preventing H2S cracking in metallic materials by industry organizations such as API and IOGP and national and international codes such as ANSI, EN, and ISO. NACE MR0175 is a method for preventing cracking of metallic materials exposed to H2S, according to the Code of Federal Regulations and the UK Health and Safety Executive.
NACE MR0103 Materials Resistant to Sulfide Stress Cracking in Corrosive Petroleum Refining Environments was released in 2003 to address the refining sector. In 2003, ISO approved MR0175 and classified it as ISO 15156. The three components of NACE MR0175/ISO 15156 are as follows:
- Part 1: Selection of crack-resistant materials based on general concepts
- Part 2: Carbon and low-alloy steels that resist cracking
- Part 3: Corrosion-resistant alloys (CRAs) and other alloys that resist cracking
Factors that Matter in the Selection of Piping Material
If you are thinking of diving into piping system engineering services or are already involved in this, you need to know the materials selection process. You should consider the overall design philosophy, cost profile, inspection, maintenance philosophy, safety, environmental profile, failure risk analyses, and other project needs. Materials should be chosen with care to ensure safety and reliability. The following should be examined at a minimum:
- Specific operating conditions, such as start-up and shut-down, that you can take into account while calculating corrosion.
- Requirements for design life and system availability;
- Probabilities, mechanisms, and consequences of failure for human health,
- The environment, safety, and material assets;
- Brittle fracture resistance;
- Inspection and corrosion monitoring; and
- Maintenance and repair access
A thorough analysis is important to reduce overall cost and maintain safety and reliability. For this, the corrosivity of the chosen material must be determined. For this, you should take the factors into consideration like:
- CO2 content;
- H2S content;
- oxygen content and content of other oxidizing agents;
- Operating temperature and pressure;
- Organic acids (pH);
- Halide, metal ion, and metal concentration;
- Velocity, flow regime, and sand formation;
- Biological activity; and
- Condensing conditions.
What is the H2S Cracking Mechanism?
Sulfide Stress Cracking (SSC) is a type of hydrogen-induced cracking that happens in the presence of water and hydrogen sulfide when tensile stress and corrosion combine. When atomic hydrogen diffuses into metal, it gathers in internal laminations or other voids, causing SSC. Hydrogen molecules are formed when atomic hydrogen gathers at the laminations or vacancies. The amount of hydrogen absorbed and the microstructure of the material impact the degree of embrittlement.
When hydrogen embrittlement occurs, it causes a loss of ductility and load-bearing capacity, leading to cracking and brittle failures below the vulnerable materials' expected proof or yield strength. Microstructures that provide high strength, as measured by hardness, or have precise distributions of grain boundary particles or inclusions, might increase embrittlement susceptibility. Eventually, enough pressure builds up inside the void to cause a crack to form. Tensile stresses can take the form of either directly applied or residual stresses. Cold deformation and forming, welding, heat treatment, machining, and grinding can all cause residual tensions.
How are Material Considerations Helpful Here?
The pipe material specification and material description should specify the intent for use in sour service and the applicability of NACE MR0175/ISO 15156 standards when a piping component is intended to be used for sour service. For this, I am listing here a few points regarding hardness considerations, chemical composition, and bolts and fasteners.
- Hardness Requirements: Due to the likelihood of stress corrosion cracking, ASME B31.3 - para F723.4.4 (b)(6) refers to NACE MR0175/ISO 15156 - Part 2. It is used for determining the piping material hardness limit for carbon steel, low and intermediate alloy steels when exposed to cyanides, acids, acid salts, or wet hydrogen sulfide.
Carbon and low alloy steels are acceptable at a hardness less than 22 Rockwell hardness (scale C) if they contain less than 1% nickel. According to the NACE standard, certain metallurgical standards must also be met, including the control of hardness in weldments.
- Chemical Composition: The sulfur content of steel is particularly important, and ISO 15156 - Part 2 defines it. You should maintain within acceptable limits as values greater than that can cause damage to the pipes.
- Bolts and Fasteners: Because ASTM A193 Grade B7M bolting is weaker than A193 Grade B7 bolting, lower piping class pressure ratings may be required in sour service applications. You should choose a gasket with lower seating stress as an alternative.
Conclusion
Even though these assets have been exporting sweet gas, sour gas may be the sole gas available for import by the piping system and engineering services industry. Thus, a sour service assessment of the facilities and pipelines is strongly suggested in such circumstances, or if a new operator is taking over the operatorship of older assets.