Types of Pipe Joints Used in Different Piping Systems Explained
Pipe joints are the key components of a piping system. Their effective design has a major impact on the operational efficiency, service life, and maintenance of the piping system. Therefore, vital factors that you should consider in the selection of joints for any project include:
- The cost of materials
- Labor charges for installations
- The required degree of leakage integrity
- Period maintenance needs
- Specific performance requirements
- Applicable code requirements
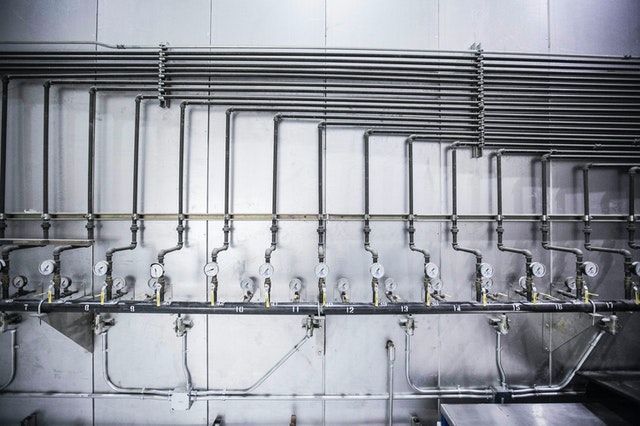
Depending on the application requirements, different joints are used in the piping system. They can be broadly classified into the following eight categories:
- Butt Welded Joint: These are the most used joints that find application in large industrial piping systems and commercial projects. Skilled fitters and pipe welders are needed for butt welding. These pipe joints offer superior strength and leakage integrity. This type of joint results in low pressure, as its inner surface is smooth and steady with a continuous flow. It is typically preferred for high-pressure-temperature applications with large bore pipes. Most piping installations are used for standard size DN 50 (NPS 2) or larger to achieve a smooth external surface.
- Socket Welded Joint: Socket welded joints are essentially used in piping systems with a high possibility of leakage. In socket welded joints, one pipe is placed inside the other. This joint is then welded from the outside. This pipe joint has a lower installation cost as compared to butt welded joints. However, the internal crevice is susceptible to corrosion. Despite this, the mechanical strength of a socket welded pipe joint is higher as compared to other types of pipe joints.
- Threaded Joint: When two adjacent pipes are connected by the screwing in threads, it is called a threaded joint. In this type of joint, one pipe has internal threads and the other has threads on the external surface. These threads can be found in different types of pipes ranging from PVC and CI to GI and copper pipes. The diameter of threaded pipe joints typically ranges from 6mm to 300mm depending on the application.
- Brazed joint: When two pipes are connected using filler material that is melted at a temperature of 840°C, the process is called brazing. Brazing is used to join copper or copper alloy pipes. It is important to ensure that the melting point of the pipe material is kept higher than that of the molten filler material. Brazed joints are commonly used in piping systems with moderate temperatures as they tend to have less mechanical strength.
- Soldered joint: The only difference between soldered and brazed joints is that filler material is melted below 840°C. During soldering, the joining material is used to avoid oxidation that occurs due to the flame. Soldered joints ensure good installation productivity and leakage integrity. This makes them ideal for use in high-purity pneumatic control installations where temperatures are low. However, their mechanical strength remains low.
- Grooved Joint: When two adjacent pipes are connected by making grooves at pipe ends using couplings or sockets, such joints are called grooved joints. They are easy to assemble and have a relatively low labor cost. This type of piping system is also easy to uninstall and reinstall for periodic maintenance. Therefore, grooved joints are mostly used in fire protection.
- Flanged Joint: This type of joint is used in pipes installed at filter plants, pumping stations, boiler rooms, and hydraulic labs. These joints are preferred for their ease of assembling and dismantling. However, the connections are expensive. A pipe with flanged ends is connected using a hard rubber washer. The flanges are fixed by threading or welding and the connection is then bolted or forged by machining by the ends. This ensures that there is no leakage even in case of rapid fluctuations in temperature.
- Compression Joint: This joint is widely used for joining the pipe without any preparations. The pipes with plain ends are connected by fixing fittings at both ends and hence, the installations are quick and cost-effective. The two ends are joined using couplings or threaded fittings. They are then placed properly to check the pressure of the flow and see if any leakage occurs. The fittings are available in different material types depending on the project requirements.
How a Piping System Design Services Provider Can Assist Your Efforts
A piping design company has all the necessary resources along with technical acumen to assist your engineering efforts. Their interdisciplinary engineering support covers every aspect of your project including corrosion resistance, pressure drop, thermal expansion, pump activation, and flow control.
Backed by experience, they are fully equipped to solve and avoid myriad challenges that crop up during the design stage. Their end-to-end support and team of core discipline engineers also assist you with unforeseen situations and issues that may not be evident at the outset of the design project.
Whether your project requirement is for a simple pipe spool design or a complex piping system in a processing plant, a piping system design services provider can help you complete your project in a stipulated timeline while ensuring safety, compliance, accuracy, and cost benefits!